Arbeitsgruppen
Arbeitsgruppen |
Arbeitsgruppe am Höchstleistungsrechenzentrum Stuttgart
Am Höchstleistungsrechenzentrum Stuttgart (HLRS) sind durch die Vielzahl unterschiedlicher Architekturen breite Erfahrungen in der Optimierung von Simulationscodes aus vielen Bereichen vorhanden. Entwicklungen wie die im Projekt zu verwendende Bibliothek „Abstract Data and Communication Library“ ADCL [HLRS4], ebenso wie eigene Werkzeuge, beispielsweise PACX-MPI für hybride Parallelisierung zwischen zwei oder mehr Maschinen [HLRS5] oder Marmot, einem MPI Analyse und Checking Tool [HLRS6], unterstützen die Anwender. In vielen Kooperationen und Aktivitäten werden den Nutzern Konzepte und Methoden zur effizienten Nutzung moderner Architekturen im Hoch- und Höchstleistungsbereich vermittelt und gemeinsam umgesetzt.
Um auf einer vorgegeben Hardware eine Performance zu erzielen, die möglichst nahe an der theoretischen Peak-Performance liegt, müssen heutzutage viele Personen-Monate oder gar -Jahre auf die Optimierung verwendet werden. Gerade für Distributed Memory Parallelisierung (DMP) mittels MPI ist dieses Unterfangen mühsam, da MPI für jedes Kommunikationsmuster (Nachbarschaftskommunikation, kollektiv, …) eine Vielzahl von möglichen Funktionen zur Verfügung stellt, von denen der Nutzer die geeignetste auswählen sollte. Welches die geeignetste ist, ist allerdings abhängig vom jeweiligen Anwendungsfall und der jeweiligen Hardware-Konfiguration in Bezug auf Prozessor-, Memory- und Netzwerk-Setup, aber auch vom Nutzungsmodell (Time-Sharing oder dediziert). In [HLRS9] wurde der Nutzen von ADCL am Beispiel eines parallelen Gleichungssystemlösers für fünf verschiedene Architekturen untersucht. Es zeigte sich unter anderem, dass für eine bestimmte Problemgrösse bei Verwendung der performantesten MPI- Implementierung einer Architektur auf einer anderen, verglichen mit der dortigen performantesten Implementierung, eine bis zu 90%ige Erhöhung der Laufzeit möglich ist. Desweiteren sind die Optimierungen nicht portabel und Einflüsse, die zur Laufzeit auftreten, werden nicht berücksichtigt. Solche laufzeitabhängigen Faktoren sind zum Beispiel die durch das Batchsystem zugewiesenen Prozessoren, die Ressourcen-Auslastung, d.h. ob sich mehrere Programme einen Netzwerk-Switch teilen, sowie Charakteristen der Applikation, wie z.B. Message-Größen, die von den Input-Daten abhängen. Um diese Einschränkungen statisch getunter Software zu umgehen, wurde die Abstract Data and Communication Library (ADCL) [HLRS7] von der Universität Houston, USA, und dem HLRS entwickelt, um dynamisch zur Laufzeit die aktuell optimale Entscheidung zu treffen.
Sie führt erstens höhere Abstraktionsebenen für oft in Anwendungen vorkommende Kommunikationsmuster ein, stellt zweitens für jedes Kommunikationsmuster eine grosse Anzahl von verschiedenen MPI-Funktionen zur Verfügung und wählt drittens mit Hilfe von statistischen Methoden [HLRS8] zur Laufzeit diejenige MPI-Funktion aus, die unter den gegebenen Randbedingungen sowohl des Anwendungsfalls als auch der Hardware die beste Performance liefert. Das Performance und Portablität nicht im Widerspruch zueinander stehen müssen, wird in [HLRS9] deutlich.
Zu den Aufgaben des HLRS gehört es, die User bei der Nutzung der installierten HPC Maschinen zu unterstützen. Dafür werden u.a. Kurse zu verschiedensten Themen durchgeführt, um Wissen z.B. über Parallelisierung, Tools, Metacomputing oder Grundlagen wie CFD zu vermitteln. Die Kurse erreichen regelmässig Interessenten von Studenten und Doktoranden an Universitäten bis zu Forschern und Entwicklern in der Industiellen F&E.
Am HLRS besteht weitreichende Erfahrung mit unterschiedlichen zur Verfügung stehenden Architekturen. Im Multi-Core Bereich sind dies derzeit das Flaggschiff, der Bundeshöchstleistungs- rechner NEC-SX 8, und ein jüngst installiertes IBM Harpertown Cluster mit 430 Knoten mit je 8 Prozessoren in 2 Sockeln x Quadcore Harpertown. Desweiteren ist ein Cell-Cluster verfügbar.
Arbeitsgruppe am Institut für Aerodynamik und Gasdynamik der Universität Stuttgart
Die Arbeitsgruppe von Prof. Munz am Institut für Aerodynamik und Gasdynamik befasst sich seit vielen Jahren mit der Konstruktion numerischer Verfahren in der Strömungsmechanik, mit Implementierungsfragen und Anwendungen. Die Entwicklungen der letzten Jahre waren Finite-Volumen- und Discontinuous-Galerkin-Verfahren hoher Ordnung auf unstrukturierten Gittern, die zunächst zur Simulation der Schallausbreitung in komplexen Geometrien eingesetzt wurden ([IAG1], [IAG2]). In den letzten fünf Jahren wurden beide Klassen von Verfahren auch für kompressiblen Strömungen weiter entwickelt ([IAG3],[IAG4],[IAG5]) und insbesondere die Kopplung mit der Lärmberechnung untersucht ([IAG6]).
Das entwickelte Space-Time Expansion DG-Verfahren (STE-DG [IAG7], [IAG8]) und das zugehörige Rechenprogramm NSDG besitzt ein sehr flexibles Gitterkonzept und lässt sich auf allgemeinen unstrukturierten Gitter mit hängenden Knoten, mit lokalen Zeitschritten und variabler Ordnung in Raum und Zeit ausführen. Ein Beispiel ist in den Abbildungen IAG 1 bis IAG 3 gezeigt. Damit ist dieses Verfahren ideal für Strömungsprobleme mit unterschiedlichem Lösungsverhalten und einer gleichzeitigen Auflösung von Strömung und akustischem Feld. Für das NSDG Verfahren wurde eine neue Approximation der Dissipationsterme in den Arbeiten [IAG9], [IAG10] eingeführt, die in Kombination mit den lokalen Zeitschritten eine gute Effizienz auch bei der Diskretisierung von Reibungs- und Wärmeleitungstermen aufweist.
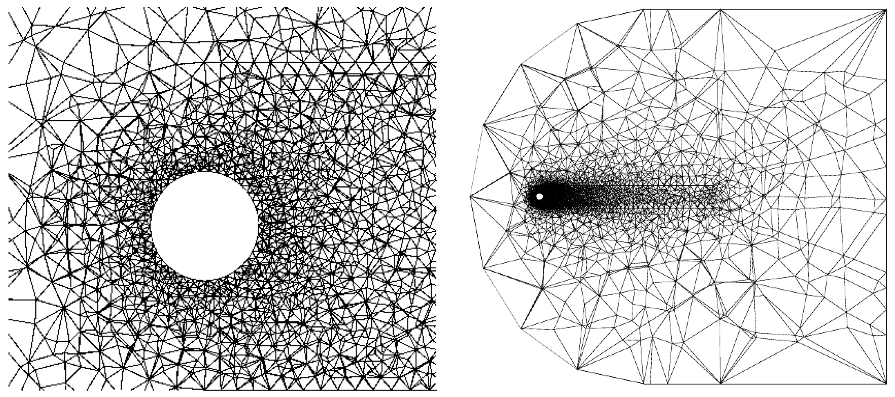
Abb. IAG1: Darstellung des Rechengitters für die Simulation einer Kugelumströmung bei M=0.3 und Re=300. Hier ein Beispiel für ein klassisches unstrukturiertes konformes Konzept mit etwa 160.000 Tetraedergitterzellen.
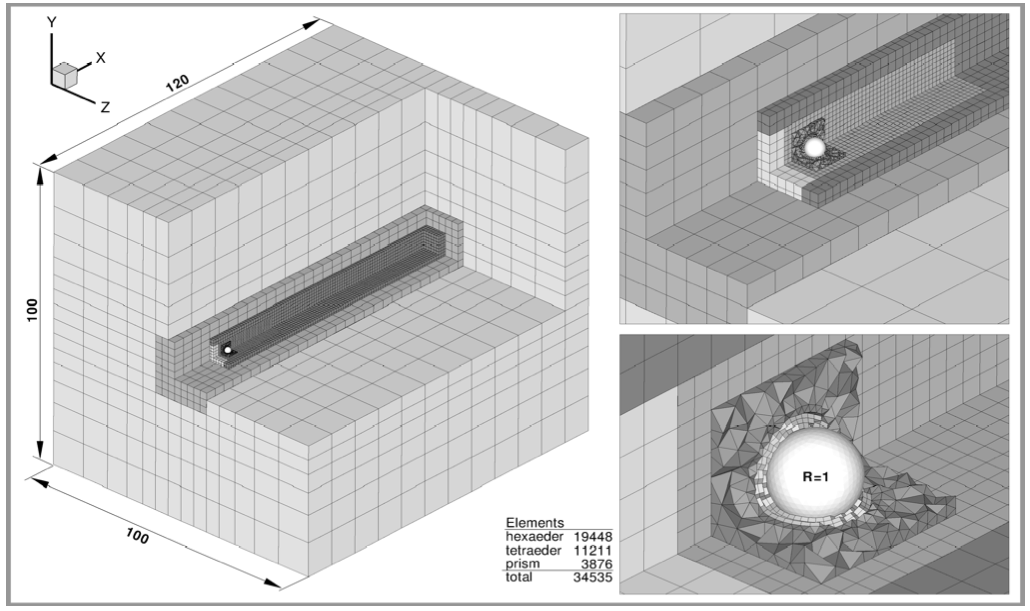
Abb. IAG2: Darstellung des Rechengitters für die Simulation einer Kugelumströmung bei M=0.3 und Re=300. Hier ein Beispiel für das neuartige Gitterkonzept mit etwa 35.000 Gitterzellen. Obwohl die Anzahl der Freiheitsgrade im Vergleich zu dem klassischen Konzept geringer ist, ist die Qualität der Lösung nahezu identisch. Die unabhängig voneinander vernetzten Blöcke werden automatisch zu einem einzigen hybriden unstrukturierten nicht-konformen Gitter zusammengefügt. Dieses „virtuelle Block unstrukturierte“ Gitterkonzept erlaubt es Gitterzellen verschiedenen Typs nahezu beliebig anzuordnen, um so die Rechnung möglichst effizient auszuführen.
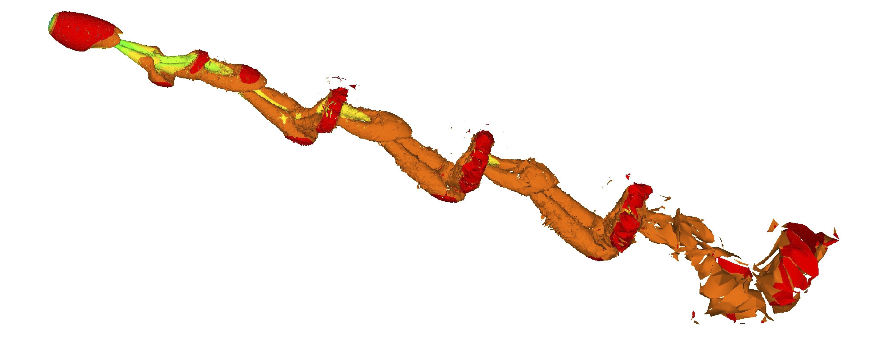
Abb. IAG3: Darstellung der Wirbelstruktur der Kugelumströmung bei M=0.3 und Re=300 mit Hilfe des Lambda 2 Kriteriums.
Arbeitsgruppe am Aerodynamischen Institut der RWTH Aachen
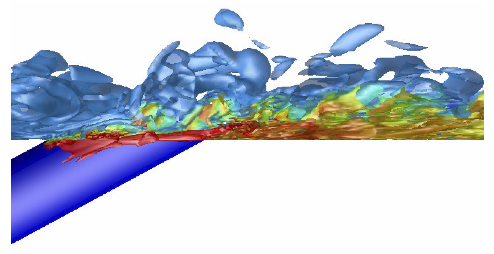
Abb. AIA1: Darstellung der turbulenten Wirbelstrukturen einer Grenzschicht-Strahlinteraktion für ein Luft/CO2 Gemisches mittels l2–Konturen. Die Farbe entspricht der CO2-Konzentration. Geschwindigkeitsverhältnis Strahlgeschwindigkeit/Außenströmung R=0.28, Massenstromverhältnis M=0.46, Reynoldszahl der Grenzschichtströmung Req=1440
Die Arbeitsgruppe am AIA in Aachen ist in Deutschland die Arbeitsgruppe, die im Rahmen von DES, LES und Grobstruktursimulation für kompressible Strömungen mit die größte Expertise hat. Aufgrund der jahrelangen Entwicklung steht ein Lösungsalgorithmus für Large-Eddy Simulationen zur Verfügung, der auf blockstrukturierten Gittern basiert, Diskretisierungen bis zur 6. Ordnung enthält und verschiedene Feinstrukturmodelle besitzt. Neben unterschiedlichen Innenströmungen [AIA7], [AIA1], [AIA9] wurden als externe Strömungen außer Freistrahlproblemen und Nachläufen stumpfer Körper turbulente Grenzschichten [AIA12] berechnet. Weiterhin wurden Grenzschicht-Strahl-Interaktionen mit und ohne Mischung unterschiedlicher Gasspezies erfolgreich berechnet [AIA2], [AIA10] (Abb. AIA1). Die Reskalierungsmethode zur Kopplung der Verteilungen des Lösungsvektors auf dem Ein- und Ausströmrand wurde für kompressible Strömungen mit Druckgradient erweitert, um Strömungen entlang von ebenen Platten, Rampen und Profilen ermitteln zu können [AIA12], wobei der detaillierte Vergleich mit numerischen und experimentellen Daten aus der Literatur die überzeugende Qualität der ermittelten Ergebnisse aufgezeigt hat (Abb. AIA2). Darüber hinaus wurde ein Verfahren zur Grobstruktursimulation mit Vorkonditionierung und Dual Time Stepping entwickelt, um nahezu inkompressible Strömungen anhand von Lösungen der kompressiblen Erhaltungsgleichungen effizient berechnen zu können [AIA10]. Aufbauend auf den ausgeprägten Erfahrungen in der Entwicklung und Anwendung von Computational Fluid Dynamics (CFD) Verfahren wurde im Rahmen des DFG geförderten Projektes SWING (Simulation of Wing-Flow Noise Generation) am Aerodynamischen Institut eine Computational Aeroacoustics (CAA) Methode entwickelt [AIA13], [AIA14]. Für die Berechnung der Schallausbreitung in homogenen Grundströmungen wurden zunächst die linearisierten Euler-Gleichungen verwendet, zu deren Approximation zwei Verfahren, das DRP- und ein Padé Verfahren, herangezogen wurden.
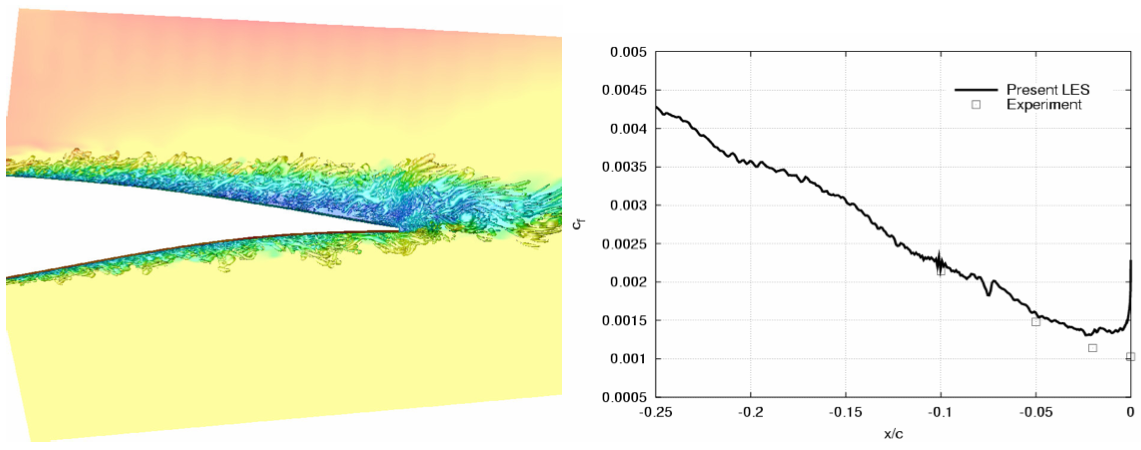
Abb. AIA2: Zonale LES einer turbulenten Strömung um eine Profilhinterkante für eine Machzahl von Ma=0.15 und einer Reynoldszahl von Re=800.000. Links: Darstellung der Wirbelstrukturen mit Hilfe des l2-Kriteriums. Die Farbe entspricht der lokalen Machzahl. Rechts: Reibungsbeiwert auf der Oberseite des Profils im Vergleich zu experimentellen Daten der Universität Stuttgart.
Für die zeitliche Integration wurde ein explizites Runge-Kutta Schema nach Hu in den CAA-Löser implementiert. Das Integrationsschema verwendet ein alternierendes 5-/6-Schritt Schema mit spektraloptimierten Koeffizienten (Low-Dissipation and Low-Dispersion Runge-Kutta Schema, LDDRK 5-6). Das Verfahren ist von vierter Ordnung genau und weist im Vergleich zu einem nicht alternierenden Verfahren eine höhere Stabilität auf. Anhand der Quelltermfilterung [AIA13] wurden die akustischen Störungsgleichungen (Acoustic Perturbation Equations, APE) entwickelt [AIA4], indem die linearisierten Euler-Gleichungen durch kombinierte Fouriertransformation im Raum und Laplacetransformation in der Zeit in den Wellenzahl / Frequenzraum überführt wurden. Es entstand ein System, in dem die Antwort der verschiedenen Eigenmoden auf den Quellterm als Komponenten eines Vektors enthalten sind. Ein modifizierter Vektor wurde gebildet, indem lediglich der Wert der Komponente der Akustikmode verwendet wurde. Durch Substitution dieses modifizierten Vektors wurde ein neuer Quellterm ermittelt, der die linearisierten Euler-Gleichungen lediglich in der nicht zu Null gesetzten Akustikmode anregt, wodurch sich ein für die reine Schallausbreitung formuliertes Störgleichungssystem ergab.
Die akustischen Störungsgleichungen wurden mit Hilfe des DRP-Schemas auf zahlreiche Probleme erfolgreich angewendet, die mit einem hybriden LES/CAA Verfahren berechnet worden sind. Neben der Bestimmung des Schallfeldes eines Kreiszylindernachlaufs [AIA4] wurde der von der Wechselwirkung zwischen einer turbulenten Strömung und der Hinterkante einer ebenen Platte (Abb. AIA3) [AIA11] sowie der Hinterkante eines Profils erzeugte Breitbandlärm ermittelt [AIA15]. Darüber hinaus wurden zur Erfassung von Verbrennungslärmmechanismen die Quelltermformulierungen der akustischen Störungsgleichungen erweitert und unter Berücksichtigung von LES-Daten das akustische Feld einer Diffusionsflamme berechnet [AIA16] (Abb. AIA4).
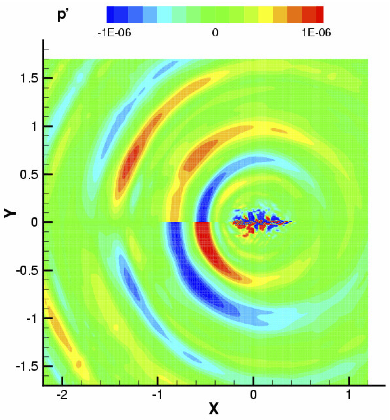
Abb. AIA3: Schallfeld einer mit der Machzahl=0.15 und der Reynoldszahl=7 ⋅ 105 umströmten Plattenhinterkante.
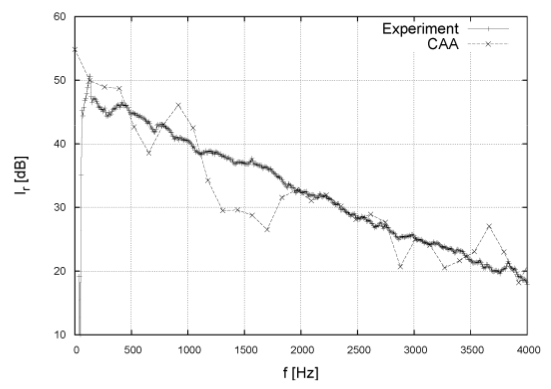
Abb. AIA4: Vergleich der numerischen und experimentellen Verteilung der radialen Intensität für eine H3-Flamme.
Insgesamt verfügen demnach die Antragsteller in den Bereichen, die für die Bearbeitung des Forschungsantrages entscheidend sind, d.h. sowohl auf dem Gebiet der Grobstruktursimulation mit und ohne Mischungsvorgänge sowie der LES auf zeitlich unabhängigen und zeitlich abhängigen Netzen als auch in dem Forschungsfeld Computational Aeroacoustics durch die Entwicklung und Anwendung der akustischen Störungsgleichungen auf Strömungs- und Verbrennungslärm, über in vielen Jahren aufgebaute Expertise.
Arbeitsgruppe der Robert-Bosch GmbH
Die Arbeitsgruppe der Robert-Bosch GmbH hat ihren Tätigkeitsschwerpunkt im Bereich von hydrodynamischen und thermodynamischen Problemstellungen. Behandelt werden sowohl Grundlagen- als auch Anwendungsthemen. Ein sehr wichtiges Gebiet in den kommenden Jahren sind gasführende Dosier- und Injektionssysteme, die z.B. in Methangasbetriebenen Kfz-Motoren Anwendung finden. Entsprechende Untersuchungen erfolgen dabei sowohl theoretisch als auch experimentell. Im theoretisch-numerischen Bereich werden aufbauend auf kommerziellen Tools wie Ansys CFX, Fluent etc. augenblicklich schon numerische Simulationen von Teilbereichen der Strömung durchgeführt. Neben normalen Workstations steht für Berechnungen auch ein Parallel- Cluster aus ca. 250 Opteron-Prozessoren zur Verfügung. Während die verwendeten Methoden prinzipiell in der Lage sind, Aussagen über stationäre und instationäre Phänomene zu liefern, bedeuten diese einen hohen Aufwand an Vorbereitung und Rechenzeit. Aufgrund dieser Schwierigkeiten kann z.B. keine systematische Auslegung von Komponenten basierend auf numerischen Simulationen erfolgen (Details siehe unten). In der Forschungsgruppe CR/ARH2 werden auch experimentelle Versuche ausgeführt, die zur Validierung der Simulationen benutzt werden. Speziell für Gasströmungen und aeroakustische Phänomene stehen z.B. Aufbauten zur Schlierenoptischen Messung zur Verfügung, bei denen Kameras wahlweise mit hoher zeitlicher oder mit hoher räumlicher Auflösung zum Einsatz kommen. Zur Auflösung stark transienter, also instationärer Phänomene wie akustischen und hydrodynamischen Druck-Fluktuationen kann u.a. Laser-Vibrometrie eingesetzt werden. Alternativ dazu können auch direkte Akustikmessungen mittels hochauflösender Mikrofone oder Drucksensoren gemacht werden. Zur Visualisierung von Mischungsverhalten können Wärmebildverfahren verwendet werden. Im Moment befindet sich ein Prüfstand im Aufbau, der es erlauben wird, sämtliche Prozesse in der Gasversorgung eines CNG-Motors exakt abzubilden und mittels der oben genannten Techniken zu vermessen.
Im folgenden soll ein kurzer Einblick in die bereits durchgeführten Vorarbeiten sowie bestehende Probleme gegeben werden. Zu diesem Zweck wird ein typisches Beispiel aus der Anwendung betrachtet (Abb. BOSCH1). Die linke Seite der Abbildung (Abb. BOSCH1a) zeigt ein heutzutage im Kfz-Bereich eingesetztes Injektionsventil für Methan, durch das während des Betriebes ein Überschall-Gasstrahl in das mit Ansaugluft gefüllte Saugrohr eines Motors strömt. Primäres Ziel der Anwendung ist eine gute Gemischbildung, da das Methan-Luft-Gemisch anschließend in die Zylinder des Kfz geleitet wird und die Gemischqualität entscheidend Eigenschaften wie Verbrennung und Emissionen bestimmt. Ein experimentell während des Betriebs oberhalb des Injektors aufgenommenes Schlieren-Bild belegt die Existenz stark fluktuierender Stoßzellen, die Quellen hoher Lärm-Emissionen darstellen. Zur numerischen Abbildung der relevanten Effekte wird in Ansys CFX ein sehr fein diskretisiertes Gitter verwendet, das in Abb. BOSCH1b zu sehen ist. Die Einblasung des Methans folgt durch die nierenförmigen öffnungen, typische Gittergrößen liegen im Bereich von 18 μm. Das Ergebnis einer LES zeigt Abb. BOSCH1c. Gut zu erkennen sind die experimentell gefundenen Stoßzellen oberhalb der Einblasöffnungen. Allerdings liegt der Aufwand einer solchen Simulation vor allem aufgrund des global sehr kleinen Zeitschrittes von 2.5e-8s bei 1400 CPU-Tagen pro Millisekunde Simulationszeit. Außerdem wird ein Spektrum bis 20MHz aufgelöst, während tatsächlich nur Lärm unterhalb 50kHz entsteht und Lärm unterhalb 20kHz für das Design überhaupt interessant ist. Insgesamt wäre es erstrebenswert, einen kompletten Einspritzzyklus, d.h. ein Zeitintervall von über 10 Millisekunden zu berechnen. Dies würde mit den gegenwärtig üblicherweise verwendeten 16 Prozessoren 3,4 Jahre dauern (in dieser Rechnung beträgt der Overhead durch Parallelisierung etwa 6 %). Eine deutliche Effizienzsteigerung ist hier zwingend nötig.
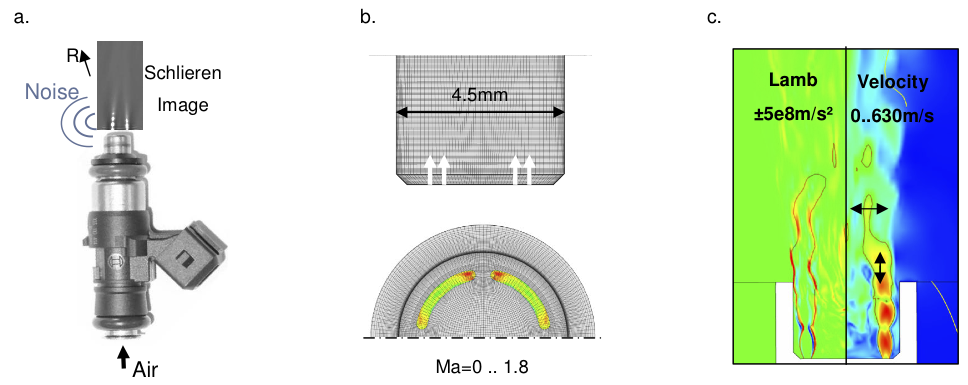
Abb. BOSCH1: Numerische Simulation einen instationären Einblas-Prozesses von Methan durch ein im Kfz- Bereich verwendetes Injektionsventil. a. Ventil-Aufbau und experimentelle aufgenommene Schlieren-Bilder. b. Numerische Diskretisierung des Auslaßbereiches und Geschwindigkeitsverteilung in den Einblas-öffnungen. c. Momentaner Lamb-Vektor (linke Bildhälfte) und Geschwindigkeitsverteilung (rechte Bildhälft) der Strömungsverteilung ermittelt durch LES.
Aufgrund der langen Rechenzeiten ist mittels der heutigen kommerziell verwendeten Methoden eine numerisch gestützte systematische ganzheitliche Auslegung und Optimierung vom Bauteilen insbesondere im Hinblick auf instationäre Phänomene (z.B. Aeroakustik) nicht möglich, da die Zahl der zu berechnenden Designs schnell die Größenordnung von 1000 erreicht. Selbst die Behandlung stationärer Effekte erfordert einen hohen zeitlichen Aufwand durch u.a. die erneute Vernetzung von geänderten Geometrien und Anpassung and neue Strahlgeometrien. Die genannten Probleme werden noch gravierender, wenn höhere Eingangsdrücke auftreten. So liegen beispielsweise typische Eingangsdrücke bei Injektionsventilen bei 7 bar, die Eingangsdrücke von Reduzierventilen jedoch bei 200 bar. In letzterem Kontext spielen auch Realsgaseffekte eine deutlich bedeutendere Rolle. Um eine erste Einschätzung der Effizienz von DG-Verfahren mit adaptivem Zeitschritt in Vergleich zu kommerziellen Verfahren zu gewinnen, wurden in Kooperation zwischen Robert Bosch GmbH und IAG erste Rechnungen an einem einfachen 2D-Freistrahlbeispiel durchgeführt. Abb. BOSCH2 zeigt das momentane Geschwindigkeitsfeld eines Freistrahl-Beispiels berechnet a. mit Ansys CFX und b. mit einem NSDG-Verfahren. Während die herkömmliche LES mittels Ansys CFX 252 CPU-Tage für eine Simulationszeit von einer Millisekunde benötigt, erreicht das NSDG Verfahren auf dem gleichen Netz 18 CPU-Tage pro ms. Die Abbildung deutet zudem an, dass die per NSDG-Verfahren errechnete Lösung deutlich mehr Details bietet (z.B. Scherschicht-Instabilitäten) und damit in ihrer Qualität außerdem höher zu bewerten ist.
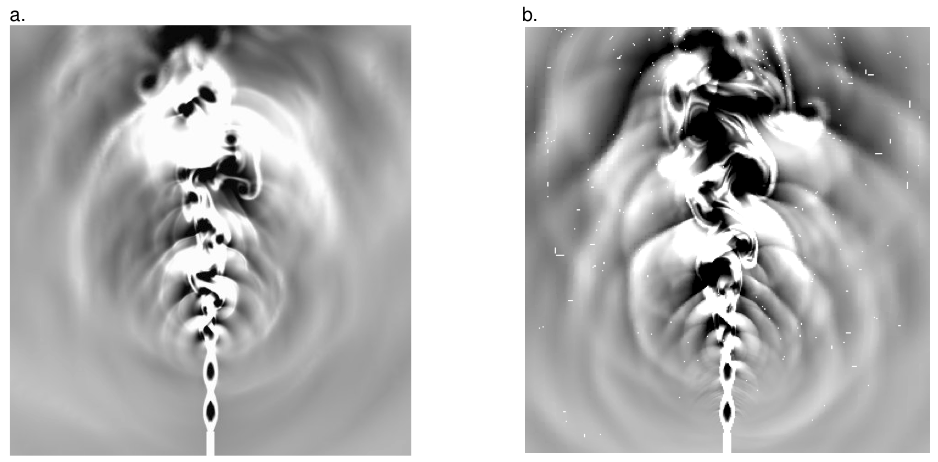
Abb. BOSCH2: Simulation eines instationären Freistrahlexperiments, Mach-Zahl Ma=1.4, Reynolds-Zahl Re = 30000, mittels a. Ansys CFX, b. NSDG-Verfahren.
Zusammenfassend lässt sich der derzeitige Stand der Vorarbeiten bei der Robert-Bosch-GmbH daher wie folgt beschreiben: Insgesamt ist ein breit gestreutes Know-How zu verschiedenen hydrodynamischen und thermodynamischen Problemen sowohl auf theoretischer, numerischer als auch auf experimenteller Seite vorhanden. Im Bereich einiger technisch relevanter Systeme wie Einblasventile für Methan wurden bereits stationäre und instationäre Berechnungen des Strömungsfeldes im wesentlichen auf Basis kommerziell verfügbarer Tools als auch Messungen zur Validierung durchgeführt. Die Ergebnisse sind von der Qualität her zwar je nach Anwendung akzeptabel bis hin zu recht gut, erlauben aber aufgrund der extrem langen Rechenzeiten keine systematische Optimierung. Für andere Applikationen (z.B. Reduzierventile) wird mit einer deutlichen Zunahme der Schwierigkeiten gerechnet. Erste sehr einfache Testrechnungen mit DG-Verfahren deuten ein hohes Potential zur Lösung der genannten Probleme an.
Arbeitsgruppe der TRUMPF Werkzeugmaschinen
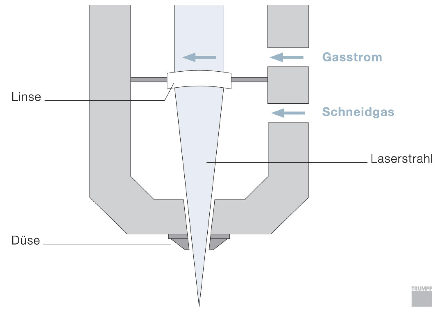
Abb. TRUMPF1: Prinzipieller Aufbau eines Linsenschneidkopfes.
TRUMPF beschäftigt sich seit über 20 Jahren mit der Entwicklung von Laserschneidköpfen für die Blechbearbeitung. Dabei hat der Schneidkopf beim Laserstrahlschneiden zwei Hauptaufgaben zu erfüllen: Einerseits nimmt er die Optik auf, mit der der Laserstrahl auf das Werkstück fokussiert wird. Andererseits sorgt er für die Schneidgasströmung, mit der die Schmelze aus dem Schnittspalt getrieben wird. Innerhalb der letzten zwei Jahrzehnte hat sich der grundlegende Aufbau eines Laserschneidkopfes nicht verändert. Bei diesem Schneidkopfkonzept wird der Laserstrahl mittels einer Linse auf die Werkstückoberfläche fokussiert, weshalb diese Köpfe auch als Linsenschneidköpfe bezeichnet werden. Gleichzeitig ermöglicht das Linsenschneidkopfkonzept auch noch, dass der zum Austrieb der Schmelze benötigte Schneidgasdruck zwischen Fokussierlinse und Düse aufgebaut werden kann. Abbildung TRUMPF1 zeigt den prinzipiellen Aufbau eines solchen Schneidkopfkonzeptes.
Der dabei benötigte Schneidgasdruck hängt dabei in erster Linie vom Schneidprozess ab. Beim Laserstrahl-Brennschneiden, bei dem als Schneidgas Sauerstoff verwendet wird, liegt der Druck in der Regel um die 2 bar absolut. Wird Stickstoff anstelle von Sauerstoff als Schneidgas verwendet, spricht man vom Laserstrahl-Schmelzschneiden. Der Schneidgasdruck liegt hierbei für die meisten Anwendungen zwischen 15 und 26 bar absolut.
Ein weiterer Vorteil des Linsenschneidkopfkonzeptes liegt in der Möglichkeit, einfach aufgebaute Lochdüsen zu verwenden, bei denen der Schneidgasstrahl koaxial zum Laserstrahl ausströmt. Diese Lochdüsen bestehen aus einem konisch zulaufenden Teil, an den sich dann ein zylindrischer Anteil anschließt. Die zur Anwendung kommenden Düsen unterscheiden sich dabei im Durchmesser des zylindrischen Anteils. Der Durchmesser richtet sich dabei nach dem Schneidprozess (Brennschneiden oder Schmelzschneiden) und nach der zu schneidenden Blechstärke. Die Auslegung des Durchmessers erfolgte dabei experimentell durch Schneidversuche.
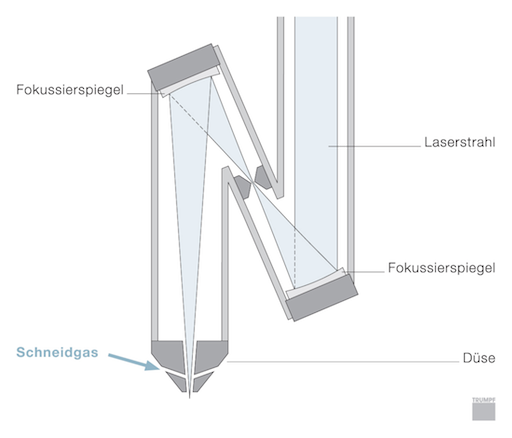
Abb. TRUMPF2: Prinzipieller Aufbau eines Spiegelschneidkopfes.
Der Trend geht beim Laserstrahlschneiden von Blechen zu höheren Schneidgeschwindigkeiten und zu stärkeren Blechstärken. Um diesen Anforderungen nachzukommen, werden immer leistungsstärkere CO2 Schneidlaser entwickelt. Diese Schneidlaser benötigen ein neues Schneidkopfkonzept, denn die Absorption der Zink-Selenid Linsen begrenzt die Laserleistung, die durch einen Linsenschneidkopf geschickt werden kann. Somit wird ein Schneidkopfkonzept notwendig, bei dem die Fokussierlinse durch einen Spiegel ersetzt wird. Diese Schneidköpfe werden als Spiegelschneidköpfe bezeichnet. Abbildung TRUMPF2 zeigt den prinzipiellen Aufbau eines Spiegelschneidkopfes.
Der Wegfall des transmissiven Elementes in einem Spiegelschneidkopf sorgt jedoch dafür, dass die heute eingesetzten Lochdüsen nicht verwendet werden können. Dies macht die Entwicklung sogenannter Ringspaltdüsen notwendig. Bei Ringspaltdüsen wird der Kesseldruck nicht wie bei den Lochdüsen zwischen Linse und Düsenmund, sondern in einer den Laserstrahl umgebenden Ringkammer aufgebaut, aus der das Schneidgas durch einen ringförmig ausgebildeten Kanal Richtung Laserstrahlachse strömt. Dabei werden an die Gestaltung des Ringkanals, bzw. die Schneidgasströmung, hohe Anforderungen gestellt. Eine gute Düse zeichnet sich aus durch
- einen hohen Hauptstromanteil, d.h. der allergrößte Teil des Schneidgases strömt Richtung Werkstückoberfläche und nicht Richtung Laser.
- eine Bauform, die dafür sorgt, dass das Schneidgas nicht durch andere Gase verunreinigt wird. Eine Verunreinigung des Schneidgases kann bspw. dadurch erfolgen, dass die Düse Gas aus dem Schneidkopf bzw. der Strahlführung ansaugt oder durch Wirbel, nachdem das Schneidgas aus dem Düsenmund ausgetreten ist.
- geringe Druckverluste zwischen Ringkammer und Werkstückoberfläche (Stoßkonfigurationen innerhalb der Düse).
- eine gute Schutzwirkung gegen Partikel, die Richtung Fokussierspiegel fliegen wollen.
- eine hohe erzielbare Schneidgeschwindigkeit mit gleichzeitig sauberen Schnittflanken am Werkstück.
Zum Einstellen einer Schneidgasströmung, die obige Punkte erfüllt, gibt es eine Vielzahl von Stellschrauben, angefangen über Winkel- und Durchmesservariationen bis zu unzähligen Längenverhältnissen. Dabei müssen die Stellschrauben nicht nur für das Brennschneiden und das Schmelzschneiden, sondern auch für die jeweiligen Blechdicken angepasst werden. Für eine experimentelle Düsenentwicklung müssten nicht nur eine Vielzahl von Düsen gefertigt, sondern auch gasdynamisch und schneidtechnisch untersucht werden. Allein die schneidtechnischen Untersuchungen sind sehr zeitintensiv und mit erheblichen Kosten verbunden. Daher sind neben experimentellen Düsenuntersuchungen auch gasdynamische Simulationen zwingend notwendig.
Für die rotationssymmetrischen, komplexen Düsengeometrien ohne Schnittspalt (2D Fall) können bereits Strömungen im instationären Fall recht gut berechnet werden. Begleitende Experimente zeigten jedoch, dass ohne Berücksichtigung des Schnittspaltes nur bedingt Aussagen über das Schneidverhalten der Düse getroffen werden können. Gerade die Punkte hohe Schneidgeschwindigkeit in Kombination mit sauberen Schnittflanken am Werkstück sind somit bislang nicht numerisch auflösbar, stellen aber das essentielle Beurteilungsmerkmal einer Laserstrahlschneiddüse dar. Um zu weitere Aussagen zu gelangen, muss der Schnittspalt in die Simulation mit einbezogen werden. Beim Übergang auf dreidimensionale Berechnungen ergibt sich das Problem, dass an vielen Stellen des großen Rechengebietes sehr kleine Gitterzellen benötigt werden. So beträgt bspw. der Ringspalt an seiner kleinsten Stelle nur wenige zehntel Millimeter, dagegen ist der Abstand zwischen Blechunterkante und der Stelle, an der das Schneidgas in die Düse einströmt mehrere Zentimeter. Die Auflösung der Geometrie erfordert somit, dass für die numerische Simulation des gesamten Vorgangs bis zu 107 Zellen benötigt werden. Die kleinen Zellen bestimmen in einem üblichen instationären Verfahren den Zeitschritt und erhöhen so erheblich die Rechenzeiten, dass eine Simulation in der Praxis nicht in Frage kommt. Es wird aber vermutet, dass gerade die instationären Prozesse der entscheidende Faktor für eine gute Schneidqualität sind.